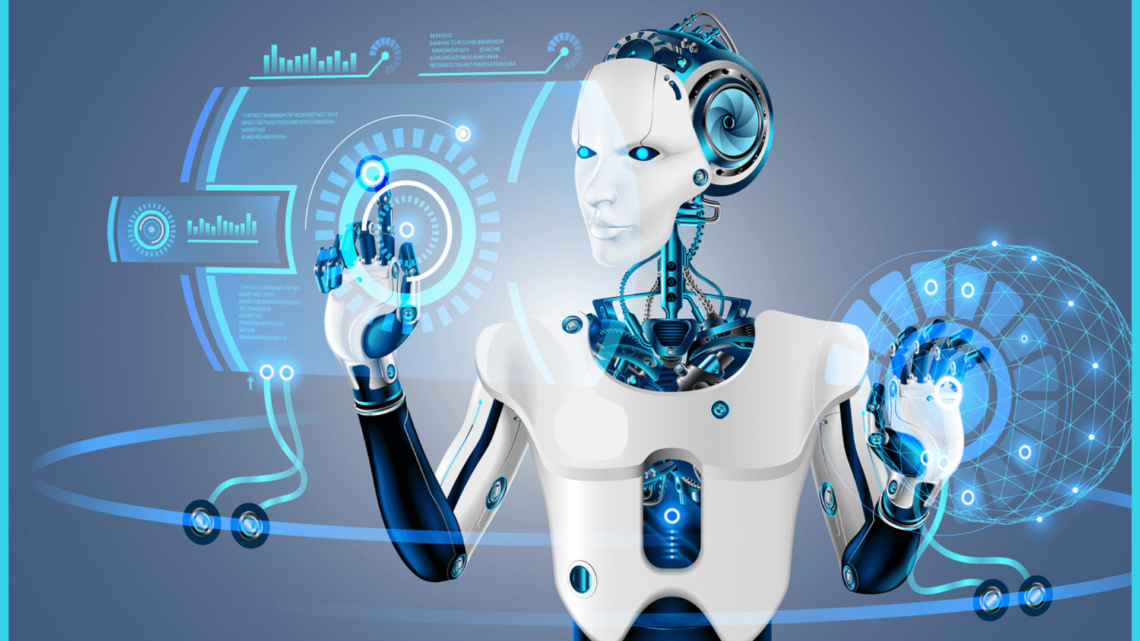
In recent years, the manufacturing industry has witnessed a significant transformation driven by advancements in technology. One of the most impactful innovations is Robotic Process Automation (RPA), which is revolutionizing the way manufacturing processes are managed and executed. By automating repetitive and mundane tasks, RPA is enabling manufacturers to increase efficiency, reduce costs, and improve overall productivity.
What is Robotic Process Automation?
Robotic Process Automation refers to the use of software robots or “bots” to automate routine tasks that were previously performed by human workers. These tasks often include data entry, inventory management, invoice processing, and quality control. RPA bots are designed to interact with existing systems and applications, mimicking human actions to perform tasks accurately and efficiently.
Key Benefits of RPA in the Manufacturing Industry
- Increased Efficiency and ProductivityRPA allows manufacturers to streamline their operations by automating repetitive tasks, freeing up human workers to focus on more strategic activities. This leads to increased productivity as tasks are completed faster and with fewer errors. For example, RPA can automate the process of updating inventory records, ensuring that stock levels are accurately maintained in real-time.
- Cost ReductionBy automating manual tasks, RPA reduces the need for human intervention, leading to significant cost savings in terms of labor expenses. Additionally, RPA minimizes the risk of errors that can lead to costly rework or product recalls, further reducing operational costs.
- Improved Quality ControlIn the manufacturing industry, maintaining high-quality standards is crucial. RPA enhances quality control processes by automating inspections and testing procedures. Bots can perform repetitive quality checks consistently and accurately, identifying defects early in the production process and reducing the likelihood of defective products reaching customers.
- Enhanced Supply Chain ManagementRPA plays a vital role in optimizing supply chain operations. By automating tasks such as order processing, shipment tracking, and inventory management, RPA ensures that the supply chain operates smoothly and efficiently. This leads to improved customer satisfaction as orders are fulfilled accurately and on time.
- Scalability and FlexibilityOne of the significant advantages of RPA is its scalability. Manufacturers can easily scale their operations by deploying additional bots as needed, without the need for extensive training or onboarding. This flexibility allows manufacturers to adapt to changing market demands quickly and efficiently.
Use Cases of RPA in the Manufacturing Industry
- Inventory ManagementRPA bots can automatically update inventory levels, track stock movements, and generate reports, ensuring that manufacturers have accurate and up-to-date information about their inventory. This reduces the risk of stockouts or overstocking and enables better demand forecasting.
- Order ProcessingBy automating order processing, RPA ensures that orders are accurately entered into the system, reducing the risk of errors and delays. This leads to faster order fulfillment and improved customer satisfaction.
- Invoice ProcessingRPA can streamline the invoice processing workflow by automating data extraction, validation, and entry. This reduces the time and effort required to process invoices, leading to faster payment cycles and improved cash flow management.
- Quality AssuranceRPA bots can perform repetitive quality checks consistently, ensuring that products meet the required quality standards. This reduces the likelihood of defects and enhances customer satisfaction.
Challenges and Considerations
While RPA offers numerous benefits to the manufacturing industry, there are challenges to consider. Implementing RPA requires a strategic approach, including selecting the right processes for automation, integrating RPA with existing systems, and ensuring that the workforce is adequately trained to work alongside bots.
Additionally, manufacturers must address concerns related to data security and privacy, as RPA involves handling sensitive information. Implementing robust security measures and ensuring compliance with industry regulations is essential to mitigate these risks.
5 Industries Where RPA Automates Operations
Robotic Process Automation (RPA) is transforming industries by automating repetitive, rule-based tasks, allowing businesses to focus on higher-value activities. From improving efficiency to reducing costs, RPA is being adopted across various sectors. Here are five industries where RPA is making a significant impact:
1. Banking and Finance
The banking and finance industry is highly regulated and involves numerous repetitive processes, making it an ideal candidate for Robotic Process Automation.
Applications:
- Account Opening and KYC: RPA can automate the customer onboarding process by handling Know Your Customer (KYC) procedures, verifying customer information, and managing account setup.
- Loan Processing: Bots can automate loan applications by collecting and validating data, reducing processing time and human error.
- Fraud Detection: RPA can monitor transactions in real-time to detect fraudulent activities, enhancing security and compliance.
Benefits:
- Efficiency: Faster processing times and reduced manual workload.
- Accuracy: Minimized errors in data handling and compliance reporting.
- Customer Experience: Improved service delivery with quicker response times.
2. Healthcare
In healthcare, Robotic Process Automation streamlines operations, allowing healthcare professionals to focus more on patient care rather than administrative tasks.
Applications:
- Patient Scheduling: Automating appointment scheduling and reminders to reduce no-shows and optimize clinic operations.
- Claims Processing: RPA can handle insurance claims by extracting and validating data, ensuring faster reimbursement.
- Electronic Health Records (EHR): Automating the updating and management of patient records for accuracy and compliance.
Benefits:
- Operational Efficiency: Streamlined administrative processes and reduced workload for staff.
- Patient Care: More time for healthcare professionals to focus on patient interactions.
- Cost Reduction: Lower operational costs due to decreased manual effort.
3. Retail
The retail industry faces intense competition, and Robotic Process Automation helps businesses streamline their operations and enhance customer satisfaction.
Applications:
- Inventory Management: RPA can automate stock monitoring and reordering processes to ensure optimal inventory levels.
- Order Fulfillment: Bots can handle order processing, tracking, and customer notifications to improve delivery times.
- Customer Support: Automating responses to common queries and processing returns and refunds efficiently.
Benefits:
- Supply Chain Efficiency: Improved inventory control and faster order processing.
- Customer Satisfaction: Enhanced service with timely updates and efficient support.
- Cost Savings: Reduced labor costs and improved accuracy in operations.
4. Telecommunications
The telecommunications industry involves complex processes that can benefit significantly from Robotic Process Automation.
Applications:
- Network Management: Automating network monitoring and maintenance tasks to ensure optimal performance.
- Billing and Invoicing: RPA can handle billing processes, reducing errors and ensuring timely payments.
- Customer Onboarding: Automating the setup of new accounts and services for quicker activation.
Benefits:
- Improved Service Delivery: Faster response times and reduced downtime.
- Accuracy: Fewer errors in billing and account management.
- Scalability: Ability to handle increasing volumes of transactions without additional resources.
5. Manufacturing
Manufacturers leverage Robotic Process Automation to optimize operations and improve productivity.
Applications:
- Production Planning: Automating data analysis and scheduling to optimize resource allocation and production timelines.
- Supply Chain Operations: RPA can streamline order processing, vendor communication, and logistics management.
- Quality Control: Automating inspection and reporting tasks to maintain high product quality.
Benefits:
- Increased Efficiency: Streamlined processes and reduced manual intervention.
- Cost Reduction: Lower operational costs and improved resource utilization.
- Quality Assurance: Consistent quality control and compliance with industry standards.
Are RPA and Workflow Automation the Same?
Robotic Process Automation (RPA) and Workflow Automation are two distinct technologies that play vital roles in improving business operations. While both aim to enhance efficiency and reduce manual effort, they differ in their approach, functionality, and application. Let’s explore the differences between RPA and Workflow Automation to understand how each can benefit organizations.
Understanding Robotic Process Automation
Robotic Process Automation (RPA) refers to the use of software robots or “bots” to automate repetitive, rule-based tasks that are typically performed by humans. These tasks often involve interacting with multiple applications, extracting and processing data, and executing predefined workflows.
Key Features of RPA:
- Task Automation: RPA automates specific tasks without requiring changes to existing systems or processes.
- User Interface Interaction: Bots can interact with the graphical user interface (GUI) of applications, mimicking human actions like clicking, typing, and reading data.
- Application Agnostic: RPA can work across various applications, including legacy systems, without the need for integration.
- Rule-Based: Ideal for automating repetitive tasks with well-defined rules and predictable outcomes.
Use Cases for RPA:
- Data Entry and Migration: Automating the transfer of data between systems.
- Invoice Processing: Extracting information from invoices and updating financial systems.
- Customer Support: Automating responses to frequently asked questions or common issues.
Understanding Workflow Automation
Workflow Automation involves the automation of business processes through a series of predefined steps, enabling the seamless flow of information and tasks between people and systems. Workflow Automation focuses on optimizing end-to-end processes rather than individual tasks.
Key Features of Workflow Automation:
- Process Automation: Automates entire business processes, coordinating tasks and approvals across departments.
- Integration: Typically involves integration with various systems to facilitate data exchange and task coordination.
- Rules and Logic: Incorporates business rules and logic to manage the flow of tasks and decision-making.
- Collaboration: Facilitates collaboration among team members by streamlining communication and task assignments.
Use Cases for Workflow Automation:
- Onboarding: Automating the employee onboarding process, including document collection and approvals.
- Order Management: Streamlining order processing and fulfillment workflows.
- Compliance Reporting: Automating the collection and reporting of compliance-related data.
Key Differences Between RPA and Workflow Automation
- Scope:
- RPA: Focuses on automating individual tasks within a process.
- Workflow Automation: Aims to automate entire processes, managing the flow of tasks and information.
- Functionality:
- RPA: Primarily interacts with user interfaces to perform tasks as a human would.
- Workflow Automation: Involves process orchestration, integrating with systems to manage workflows.
- Complexity:
- RPA: Suitable for simple, rule-based tasks with high-volume transactions.
- Workflow Automation: Designed for more complex processes that involve multiple steps, decision points, and participants.
- Integration:
- RPA: Works independently of system integrations; can interact with applications at the user interface level.
- Workflow Automation: Often requires integration with existing systems to enable seamless data exchange and task coordination.
Complementary Technologies
While RPA and Workflow Automation are different, they can be complementary. Organizations can use RPA to automate specific tasks within a broader workflow, enhancing efficiency and reducing manual intervention. For example, an automated workflow may involve several human and system-driven steps, with RPA bots handling repetitive data entry tasks along the way.
Robotic Process Automation is transforming the manufacturing industry by automating repetitive tasks, improving efficiency, and reducing costs. As manufacturers continue to embrace RPA, they can expect to see enhanced productivity, improved quality control, and a more agile and responsive supply chain. By strategically implementing RPA, manufacturers can position themselves for success in an increasingly competitive market. As technology continues to evolve, the role of RPA in the manufacturing industry is set to expand, driving further innovation and growth.